Article: Methods for Deactivation of CO2 Fire Safety Systems
Lockout Valve Versus Disable Switch
Lockout Valve Versus Disable Switch – Lockout valves and disable switches are both mechanisms which allow for deactivation of automatic discharge of a fire suppression system when it is in the maintenance mode. This brief comparison is intended to provide a basic examination of these devices, and illustrate the reasons for selecting either of these devices as part of a semiconductor tool fire suppression system, and outline the proper method for implementing these devices in a fire suppression system design that complies with applicable fire codes and semiconductor industry guidelines.
KFPI provides proper installation of lockout valves, when these devices have been designed into a fire system by a third party, qualified fire safety expert. However, KFPI rarely suggests the use of lockout valves in semiconductor fire safety systems. KFPI’s answer to the question of Lockout Valve Versus Disable Switch, is that a disable switch is better.
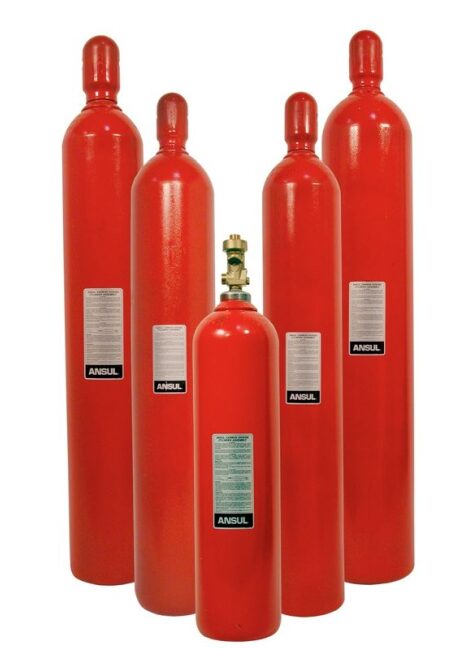
System Justifications
The basic reasons for this fire safety system design choice is as follows:
- No fire codes or industry standards require utilization of a lockout valve in a fire suppression system.
- A disable switch functions as reliably and robustly as a lockout valve, in providing the basic safety function of disabling the discharge capability of a fire suppression system during maintenance.
- A lockout valve requires secondary components to be installed, in order to comply with applicable codes – Specifically: pressure switches and pressure relief valves. (Pressure switches and pressure relief valves are required by code to be present when a lockout valve is installed.)
Install Costs
A lockout valve, properly installed, costs approximately $2500.
A disable switch, properly installed, costs approximately $350.
Applicable fire and semiconductor industry codes:
NFPA 12 2011 – Occupiable vs. Unoccupiable
- Occupiable = “If enclosure/space has dimensions such that it could be entered by a person.” (3.3.8)
- Unoccupiable = “If enclosure/space has dimensions such that it could NOT be entered by a person.” (3.3.12)
- Required except where dimensional constraints prevent personnel from entering the protected space. (4.3.3.4)
- Required where CO2 can migrate, creating hazard to personnel. (4.3.3.4.1)
OSHA (1910.147(a)(2)(ii)) – Control of Hazardous Energy
- “Energy Isolating Device” is required where any part of his or her body can be “harmed”…
- HPCO2 “Hazardous Energy” Discharge is NOT Hazardous to Personnel . ***
(***Otherwise All Pressurized Gases Would Have Same Requirements – Such as FM-200, Inert Gases, Halon, Sprinkler.)
- HPCO2 Asphyxiation Hazard / Toxic Gas Hazard
- OSHA Energy Control Not Applicable
- Default to NFPA Requirements
NFPA 12-2011 Classification As Occupiable Means:
1. Lockout Valve Must Be Installed (4.3.3.4)
2. Must Be Electronically Supervised (4.5.5)
- Pressure Switch Installed Between Supply and Lockout Valves (4.5.4.13.1)
3. Pressure Relief Valve is Required Upstream of Lockout Valve (4.7.2.3)
- Operate 2400-3000 psi (4.7.2.3.1)
4. Pneumatic Operated Controls Are Required (4.5.6.1)
- Time Delay Device Must Be Installed
- Predischarge Audio / Visual Alarm Notification Must Be Installed Within Each Enclosure
Applicable Codes and Lockout Valve Use – Conclusion:
Most Tool Protected Areas Are Un-Occupiable and Lockout Valve(+) is Not Required
- Lockout Valve Has Negative Effects On Tool Uptime
- Installed Remote From Tool in SubFab/Chase
- Creates Pressurized Entrapment Exposure (Overpressure)
- Lockout Valves Are Not Used
- Remove Actuators During Service
Service Disconnect Switch
When a Service Disconnect/Disable Switch is Required
SEMI S2 (14.4.5.10)
- Allowance for deactivation of automatic discharge of the suppression system when in the maintenance mode.
- Such deactivation switches should be supervised. (14.4.5.10)
NFPA 12 (4.5.4.12)
- For electrically operated systems, a service disconnect switch shall be provided to allow the system to be tested without actuating the fire suppression system. The service disconnect switch, when operated, shall interrupt the releasing circuit to the suppression system and shall cause a supervisory signal at the suppression system releasing panel.
- A Lockout Valve Can Act As “Service Disconnect Switch”
- Many Times This is NOT Wired Correctly.
- A Key Disconnect/Disable Switch is NOT “In Lieu” of Lockout Valve.
- May Qualify as “Energy Isolation Device” per OSHA.
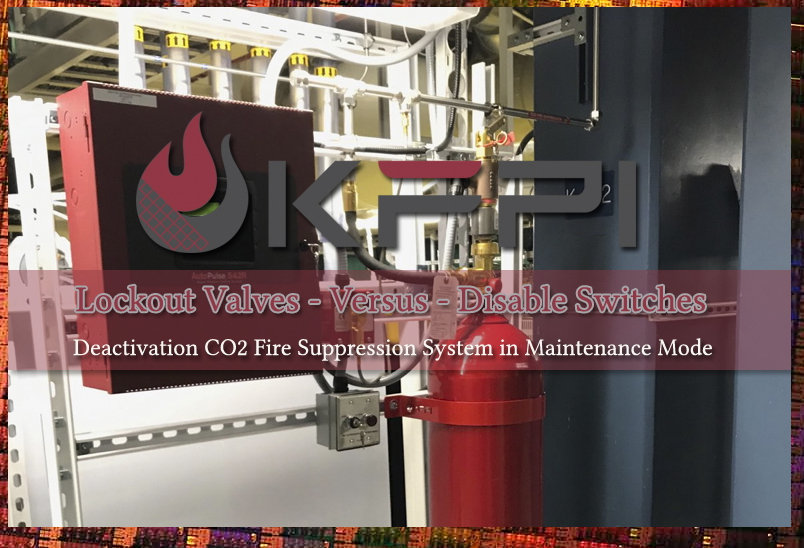
Conclusion
KFPI will install or maintain lock out valves that have been designed into fire suppression systems. KFPI will insist that all systems with lock out valves have been installed per code. If missing components such as pressure switches and pressure relief valves are missing, KFPI will insist on installing these with any fire suppression systems that use lock out valves. KFPI will only install fire suppression systems that comply with all applicable codes. Lockout valves are more expensive than disable switches, are more complicated, and perform the same service function. KFPI recommends the use of disable switches over lockout valves.