Article: Semiconductor Fire Safety Systems
Semiconductor Wet Bench FM-4910-Compliant Materials
Semiconductor wet bench systems are typically used for chemical handling in various applications, electro-chemical processing and/or acid processing, as well as other chemical wet process applications. Semiconductor wet bench equipment is made from very diverse materials like polypropylene, stainless steel, PVDF, PVC-C as well as Teflon®, PFA, and ECTFE (HALAR®). Usually, the type of material used for production of a wet bench is chosen for optimal compatibility with the process attributes as well as compatibility with the respective process chemistries. Specific material grades are required for FM4910 and UL2360 compliance. FM 4910 and UL 2360 testing protocols were adopted in the 2002 NFPA Standard 318, section A.10.5.1.2 and have driven the semiconductor industry to develop new materials used for equipment manufactured for flammable chemistry processing. If you have non-4910 plastic benches, please continue reading.
Materials passing the cleanroom protocol, subsequently, can be listed in the Approval Guide, a publication of FM Approvals. Materials that have been approved by Factory Mutual FM-4910, and have been certified include:
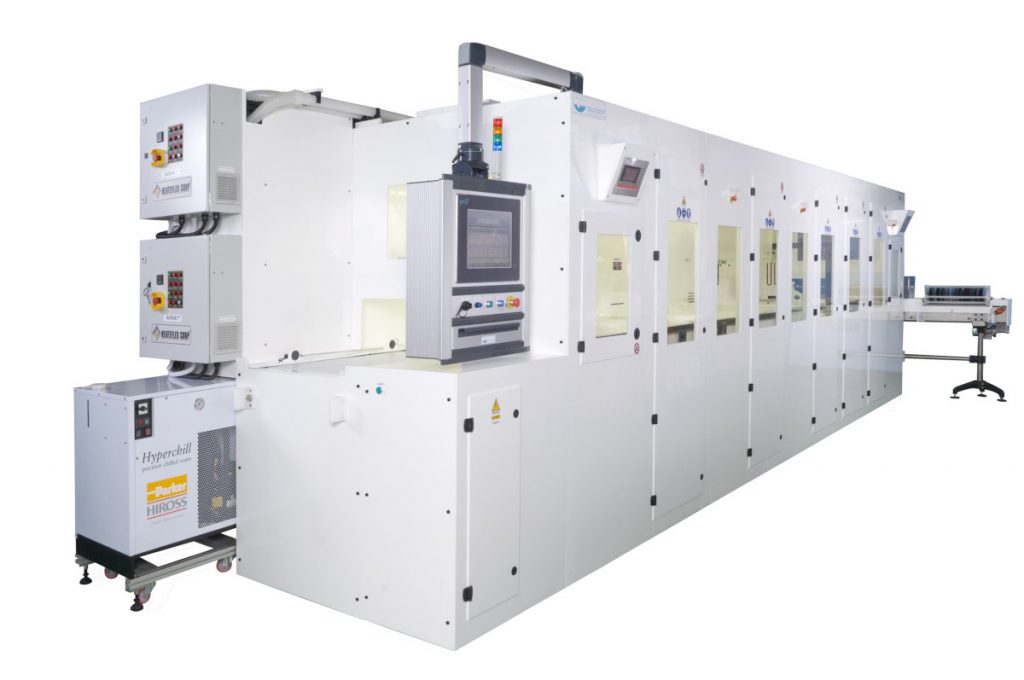
Materials passing the cleanroom protocol, subsequently, can be listed in the Approval Guide, a publication of FM Approvals. Materials that have been approved by Factory Mutual FM-4910, and have been certified include:
- Most Common
- PVC-C Polyvinylchloride
- PVDF
- Others
- CP7-D Polypropylene
- Takiron PVC and CPVC
- Boltaron PVC
- Halar
Non-FM4910 Plastic is a Fire Hazard
Plastic wet benches that are made from FM4910-compliant materials, and use flammable chemicals in the process, require fire safety systems that are code compliant. Wet benches that are made from materials that are non-FM4910 compliant, require proper fire safety systems, even if the chemicals in use are not flammable. The non-FM4910-compliant material is itself a fire safety hazard that requires proper EHS protocols. If you have a wet bench that is not made from FM4910 compliant material, then you need a fire detection and suppression system for that tool.
Preventing Cleanroom Contamination is a Paramount Goal
Contamination of cleanrooms of any kind can be catastrophic and contamination caused by fire and smoke is some of the worst. FM-4910 designation is given to a material that has passed the Factory Mutual test for fire propagation, and smoke density. The contamination caused to other processes and equipment in neighboring areas of a plastic bench fire, was the driving concern behind the FM-4910 designation. Increasing insurance costs to protect manufacturers in the event of fire and mass contamination are expensive and have driven the construction of wet benches to use less flammable materials to reduce the fire hazards already prevalent in wet bench processes. Nevertheless, there are many wet benches still in daily production use that are made from flammable plastic.
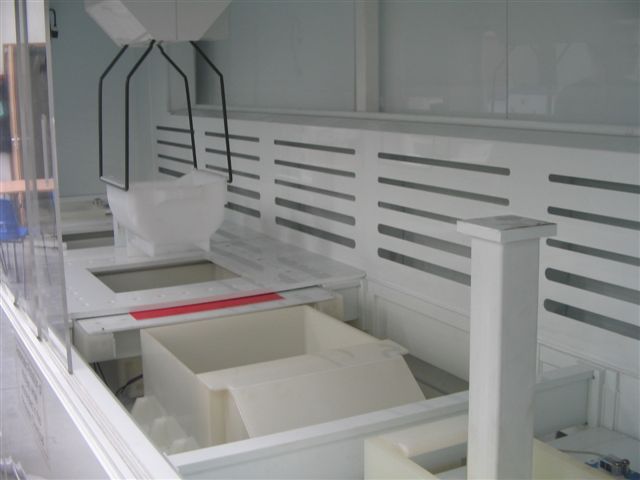
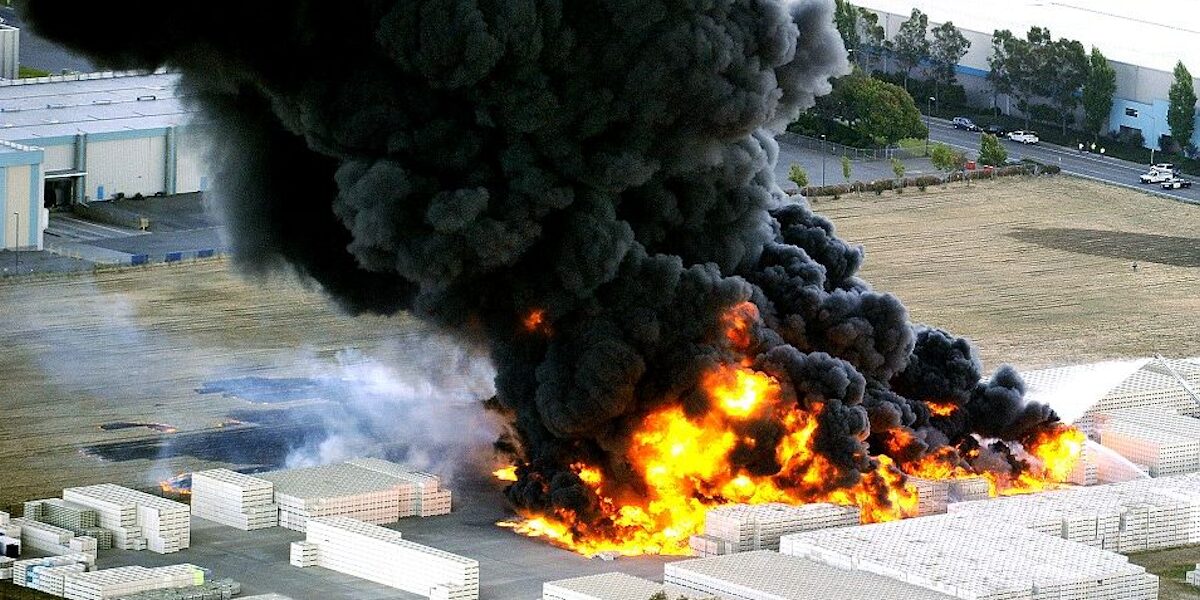
A Filthy Foe!
If you’ve ever seen plastic burn, then you know that it is dirty and dangerous. Once plastic starts burning, it REALLY burns. Aside from the obvious life safety concerns, process disruption, and potential equipment damage, even a small plastic fire in a clean room can cause BIG damage. The amount of particulates in just a small and brief plastic fire can quickly contaminate a clean room so severely as to force a complete shutdown of clean room operations.
Flammable Plastic Benches Require Fire Protection
Regardless of the type of chemistry you are using in your plastic wet station, if the plastic is not FM 4910 compliant, it poses a significant fire hazard and must be protected with a suitable fire detection and suppression system. Non-4910 plastic is a potential fuel for a fire in your clean room.
While most semiconductor wet tools are now constructed from FM 4910 compliant materials, there are many non-4910 plastic benches still used in production. These potential fuel sources for fire need to be factored into your operation’s safety strategy. When protected by a properly-designed and installed fire suppression system, this type of tool can be safely integrated into your production.
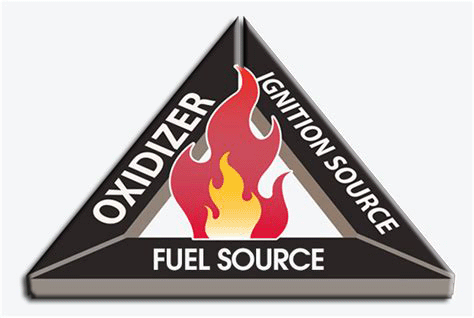
A fire requires a combination of three elements to ignite and remain burning: fuel, oxygen, and an ignition source. The oxygen provides a fire-friendly environment, the fuel will burn, and the ignition source will cause the fuel to ignite. Ignition sources include hot surfaces, electricity (including static electricity), flames, and sparks.
Fire Safety Systems for Flammable Plastic Benches
Fire safety systems for any semiconductor process equipment should be custom-designed to meet the specific safety requirements of the tool which is to be protected. Some of the most basic parameters that must be factored into the specifications of a process tool fire safety solution include the types and amounts of chemistry present in the process, the area of the potential fire hazard, the exhaust rates present at the tool, and the material of the tool construction. If the tool is made of flammable plastic, then care must be taken to design a fire safety system that not only effectively extinguishes a fire, but robustly limits to a minimal amount the smoke particles which could be released in the event of a fire. Fire extinguishment is only one of the desired functions of a wet tool fire safety system in a cleanroom. Protecting the tool and the cleanroom from costly downtime is also a paramount concern to weigh when designing the proper fire safety solution.
Typically, a fire detection and suppression system for a wet process tool consists of the proper detection methodology to watch for the presence of a flame. Usually, this involves a suitable flame detector, capable of identifying the flame signature of a potential fire. (The type of flame signature will depend on the kind of fuel which is burning.) In situations where there is little to no tolerance for smoke contamination, a high-sensitivity smoke detector might be used to sniff for minute traces of smoke. The most common type of fire suppression agent used to protect semiconductor equipment is compressed CO2 gas. Fires are quickly and robustly smothered. The CO2 gas leaves no trace chemistry or particulates on the equipment, product, or in the cleanroom.
Fire safety systems that are used in any semiconductor operation should be designed specifically to meet semiconductor standards. All equipment used in such systems should be FM approved and meet all NFPA codes applicable to this type of application. Fire safety systems intended for use on semiconductor equipment should be designed, installed, and certified by semiconductor fire safety experts. If you have any questions about your semiconductor equipment fire safety needs, please let KFPI know your concerns. We are always happy to make the semiconductor world safer.